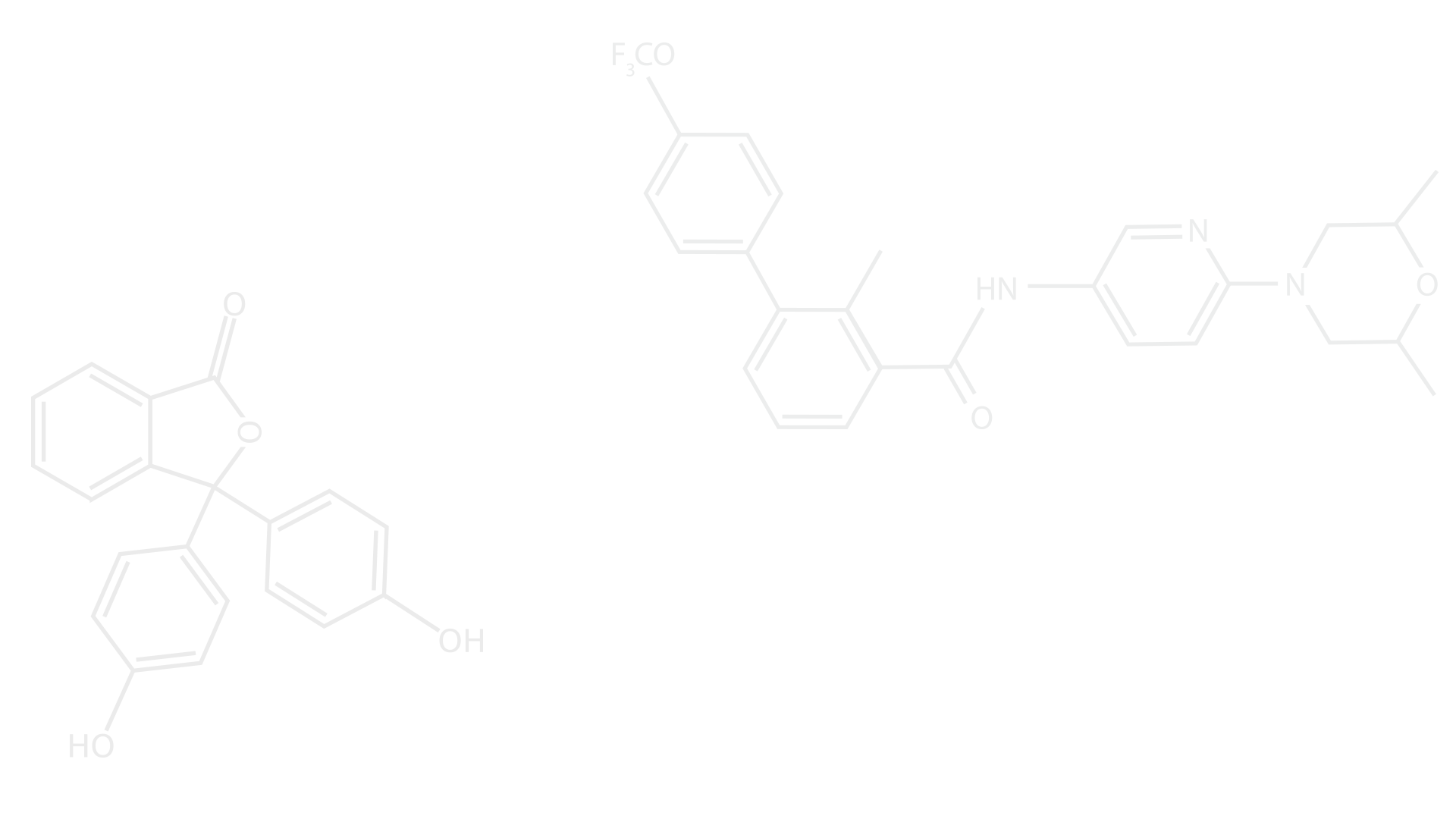
Intermediate report of phase 1
(10.10.2018 – 31.12.2018)
Main objectives:
(i) Objective analysis and acquisition of materials;
(ii) Characterization of materials / raw materials;
(iii) Coating of the fibres with resin- preliminary study;
(iv) SEM investigations - analysis of coated fibers - preliminary study.
Summary of results
​
During this stage, the characterization of the iron fibers to be used to prepare the magnetic composites based on the iron fibers was accomplished. It was established, on the basis of the analysis bulletin provided by the manufacturer, that the fibers have a satisfactory purity. This was it confirmed by X-ray diffractions that did not reveal the existence of other phases except iron.
The SEM analyzes showed that the fibers are shaped like a sectioned cylinder and that each fiber contains along the longitudinal axis two types of surfaces with completely different morphology: (i) a flat surface with low roughness; (ii) a curved surface with high roughness.
FTIR, TG and DSC analyzes revealed the contamination of the fiber surface with an organic compound. It has been shown that this compound can be successfully removed by a degreasing operation. The use of these fibers will always involve a degreasing step before any coating operation.
In order to increase the presability of these fibers, a recrystallization treatment can be carried out at temperatures above 480 ºC, the temperature determined in the DSC analyzes.
The fiber coating was made by immersing them in a solution of Araldite dissolved in acetone. The success of the coating operation was demonstrated by EDX analyzes that showed a uniform distribution of carbon (from Araldit) on the fiber surface. In conclusion, we can state the following:
(i) the fibers correspond in terms of chemical composition to reach the purpose of the project;
(ii) the diameter of the fibers is between 70 and 120 µm;
(iii) the fibers have two types of surfaces with very different morphologies;
(iv) the fibers must undergo a degreasing operation to eliminate surface contamination before any coating operation with the electric insulator layer.
SEM-EDX Investigations

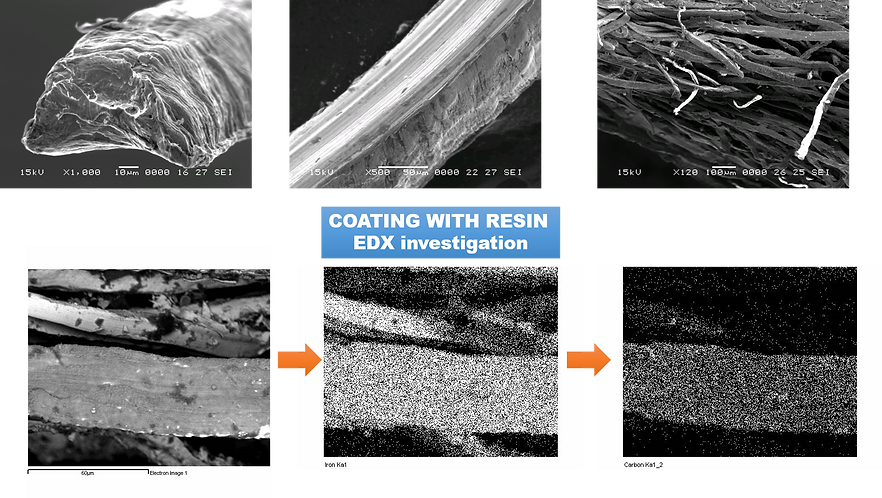
XRD Investigations

DSC Investigations

TG Investigations

FTIR Investigations

Phase number 2
(01/01/2019 - 31/12/2019)
Main objectives:
(i) FSMCs based on Fe fibres coated with resin;
(ii) FSMCs based on hybrid coated Fe fibres
Summary of the results
It was shown that long Fe fibres can be used to create soft magnetic composites. This new class of soft magnetic composites named fibre based soft magnetic composites (FSMC) presents interesting soft magnetic properties in both AC and DC magnetisation regime. The main conclusions that can be drawn from the study of the FSMCs in which the fibres are coated with polymer are: (i) In order to obtain compacts with good magnetic properties, the fibres must be heat treated prior to compaction; (ii) The polymer content and the compaction pressure plays an important role in the magnetic properties of the compacts. It was found that 1 wt.% of polymer ensures proper insulation of the fibres and the compacts must be compacted at pressures not lower than 600 MPa. (ii) The FSMC present superior DC and AC magnetic properties (in the investigated frequency range) when compared to a powder based SMC prepared in identical conditions. Future applications of these materials are dependent upon the improvements in the density of the compact as well as by the preservation of the insulating layer integrity during the compaction process. The FSMCs based on short fibres coated with polymer present interesting properties. In order to obtain good results, fibres alignment should be performed prior compaction. The best results were obtained when the fibres were aligned under the concomitant action of o vibratory movement and a magnetic field. In order to analyse the potential application of hybride coatings, two types of coating were made: Fe fibres coated with a layer of SiO2 and Fe fibres coated with SiO2 and polymer. The SiO2 layer, in both cases, was deposited via hydrothermal method. SEM and TEM investigations showed that the fibres are coated by a uniform layer of SiO2 having thicknesses in the range of 150 – 200 nm. The addition of 1 wt.% of polymer leads to an increase of the electrical resistivity of the compacts of 10%. From DC measurements we concluded that the addition of a supplementary layer of polymer on top of the SiO2 layer leads to a decrease of the saturation induction (from 1.39 T to 1.26 T), coercive field (from 367 A/m to 353 A/m) and maximum relative permeability (from 797 to 733) of the compacts. AC magnetic measurements showed that the compact based on Fe fibres coated with SiO2 exhibits lower hysteresis losses and the higher initial relative permeability. Conversely, the additional polymer layer leads to an increase of the hysteresis losses, but with the development of excessive eddy currents into the sample being prevented. The compact based on Fe fibres coated only with a SiO2 layer was subjected to an annealing which leads to a significant improvement of its magnetic characteristics.
FSMCs based on fibres coated with polymer
-
DC magnetic characterisation of the FSMCs

Hysteresis curves of an FSMC prepared from as received Fe fibres and an FSMC prepared from heat treated fibres at 650 °C for 2 hours.
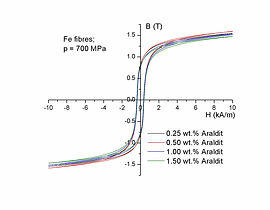

Influence of the polymer content (a) and the compaction pressure (b) over the hysteresis loops of the FSMCs
2. AC magnetic characterisation of the FSMCs

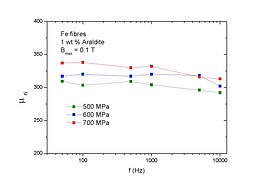


Influence of the polymer content on the core losses (a) and initial relative permeability (b) of the FSMCs in the frequency range of 50 Hz–10 kHz for Bmax = 0.1 T.
Influence of compaction pressure on the core losses (a) and initial relative permeability (b) of the FSMCs in the frequency range of 50 Hz–10 kHz for Bmax = 0.1 T.
3. Comparison of DC and AC magnetic characteristics of FSMCs and SMCs
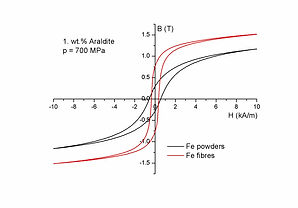


Comparison of the DC magnetic loops corresponding to an FSMC and an powders-based SMC prepared in identical conditions.
​Comparison of the AC magnetic characteristics (a - core losses and b - initial relative permeability) corresponding to an FSMC and a powder based SMC, prepared in identical conditions.
Conclusions
This new class of soft magnetic composites named fiber based soft magnetic composites (FSMC) presents interesting soft magnetic properties in both AC and DC magnetisation regime. The main conclusions that can be drawn from this study are:
-
In order to obtain compacts with good magnetic properties, the fibres must be heat treated prior to compaction;
-
The polymer content and the compaction pressure plays an important role in the magnetic properties of the compacts. It was found that 1 wt.% of polymer ensures proper insulation of the fibres and the compacts must be compacted at pressures not lower than 600 MPa.
-
The FSMC present superior DC and AC magnetic properties (in the investigated frequency range) when compared to a powder based SMC prepared in identical conditions.
Future applications of these materials, as magnetic cores, are dependent upon the improvements in the density of the compact as well as by the preservation of the insulating layer integrity during the compaction process.
FSMCs based on hybrid coated fibres

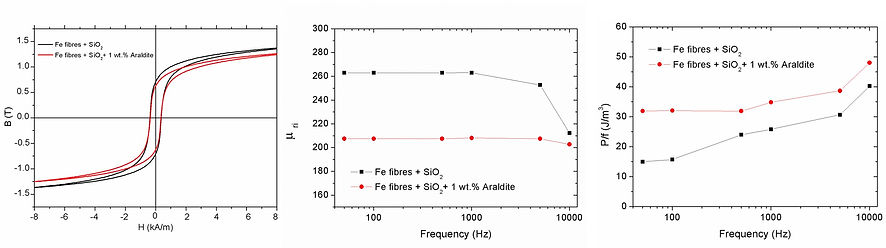
Comparison of hysteresis loops of FSMCs prepared from Fe fibres coated with SiO2 and Fe fibres coated with SiO2 and 1 wt.% polymer (Araldite).
Evolution of the total core losses (a) and initial relative permeability (b) of the compacts based on Fe fibres coated with SiO2 and, SiO2 and polymer. Bmax = 0.1 T, f = 50 Hz – 10 kHz.
Phase number 3
(01/01/2020 - 09/10/2020)
Main objectives:
(i) Fe fibres coated with soft magnetic ferrite;
(ii) Spark Plasma Sintered FSMCs.
Summary of the results
​
Soft magnetic composites (FSMCs) have been prepared by using Fe fibres coated with a layer of Fe3O4, this layer playing the role of insulating material. The coating was made via blackening method by simply immersing the fibres in the blackening bath for various duration. The formation of the Fe3O4 coating on the surface of the fibres was confirmed by X-ray diffraction. The SEM investigation, used to evaluate the thickness of the coatings. Differential scanning calorimetry and thermomagnetic measurements were used to investigate the thermal stability of the composite fibres.
The fibres coated with Fe3O4 were compacted at a compaction pressure of 700 MPa to obtain toroidal magnetic cores. The obtained cores were characterised in DC and AC magnetisation regime.
The analysis of the quasi-static hysteresis loops (DC) evidenced that increasing the thickness of the Fe3O4 leads to a slight deterioration of the compact's magnetic properties. However, as the thickness of the Fe3O4 layer increases, the development of eddy currents at a larger scale is hindered as proved by the AC magnetic investigations.
​
Also, it was proved that increasing the fibres diameter leads to FSMCs with improved DC magnetic characteristics but the AC magnetic characteristics become unacceptable for compacts based on fibres heaving the diameter of 0.5 mm due to the skin effect and the excessive development of the eddy currents.
Spark plasma sintered compacts were successfully prepared from Fe fibres coated with Fe3O4. It was proved that the SPS process have a positive influence over the DC magnetic characteristics of the compacts while the AC magnetic characteristic present a certain deterioration.
​
A model for analytic separation of the core losses is proposed. By applying this model to the prepared samples, we are now able to discriminate between the occurring losses and adjust the preparation process of new samples to the targeted characteristics.
RESULTS




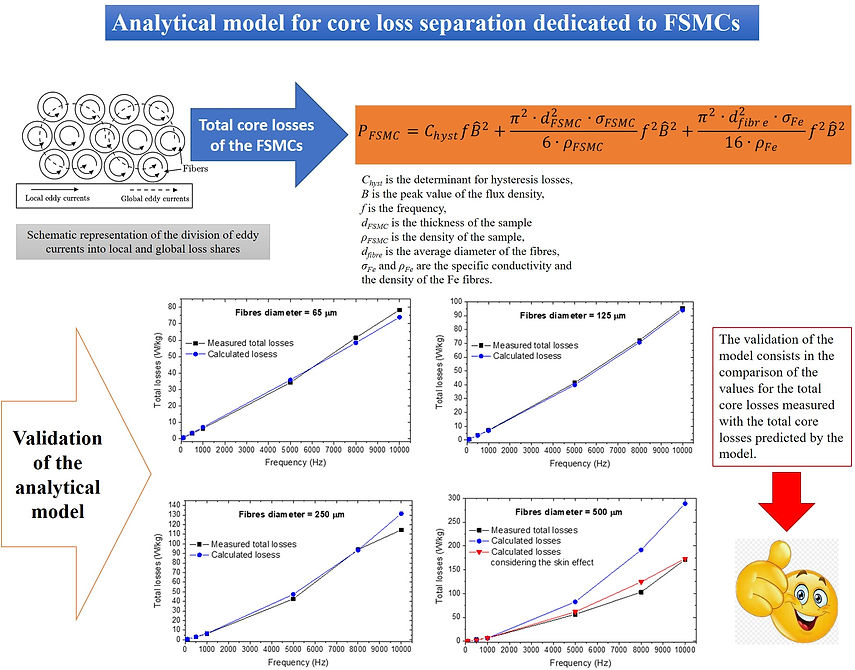
Conclusions
-
For the preparation of FSMCs based on Fe fibres coated with Fe3O4, two types of Fe fibres were used: Iron wool and Fe fibres obtained by drawing (diameter of 65, 125, 250 and 500 µm).
-
The blackening process was used to create the Fe3O4 coating, because is a quick and simple coating process that offers good quality coatings.
-
The XRD investigation proved the formation of the Fe3O4 layer on the surface of the fibres via the blackening process. The thickness and uniformity of the coating on the surface of the fibres were investigated via SEM-EDX analysis. The thickness of the coating increase as the duration of the blackening process increase.
-
The DC magnetic characteristics of the cold pressed compacts are influenced by the blackening duration and by the fibre’s diameter. Longer blackening duration leads to a decrease of DC magnetic characteristics and larger diameter of the Fe fibres leads to an enhancement of the DC magnetic characteristics.
-
Contrary, the AC magnetic properties deteriorate as the fibre’s diameter increases but ameliorates as the blackening duration increase.
-
An analytical model for core loss separation was developed and applied for the first time for the case of FSMCs. The loss separation revealed that, for the compacts based on thin fibres (65 and 125 µm) the main type of losses dissipated by the compacts is hysteresis losses while, for compacts based on ticker fibres (250 and 500 µm), upon increasing the frequency, the eddy current losses became predominant.
-
Spark plasma sintered compacts were successfully prepared from Fe fibres coated with Fe3O4. It was proved that the SPS process have a positive influence over the DC magnetic characteristics of the compacts while the AC magnetic characteristic present a certain deterioration.
-
This new type of composites can be successfully used, for example as a magnetic core for transformers, in the medium to high-frequency range. Their operation frequency range can be tuned, among others, by the thickness of fibres used for the compact preparation or by the thickness of the insulating layer.